Implant technology includes all components and devices that are intended to stay inside the body for an extended period, ranging from passive bone screws to active multichannel implants to stimulate and measure.
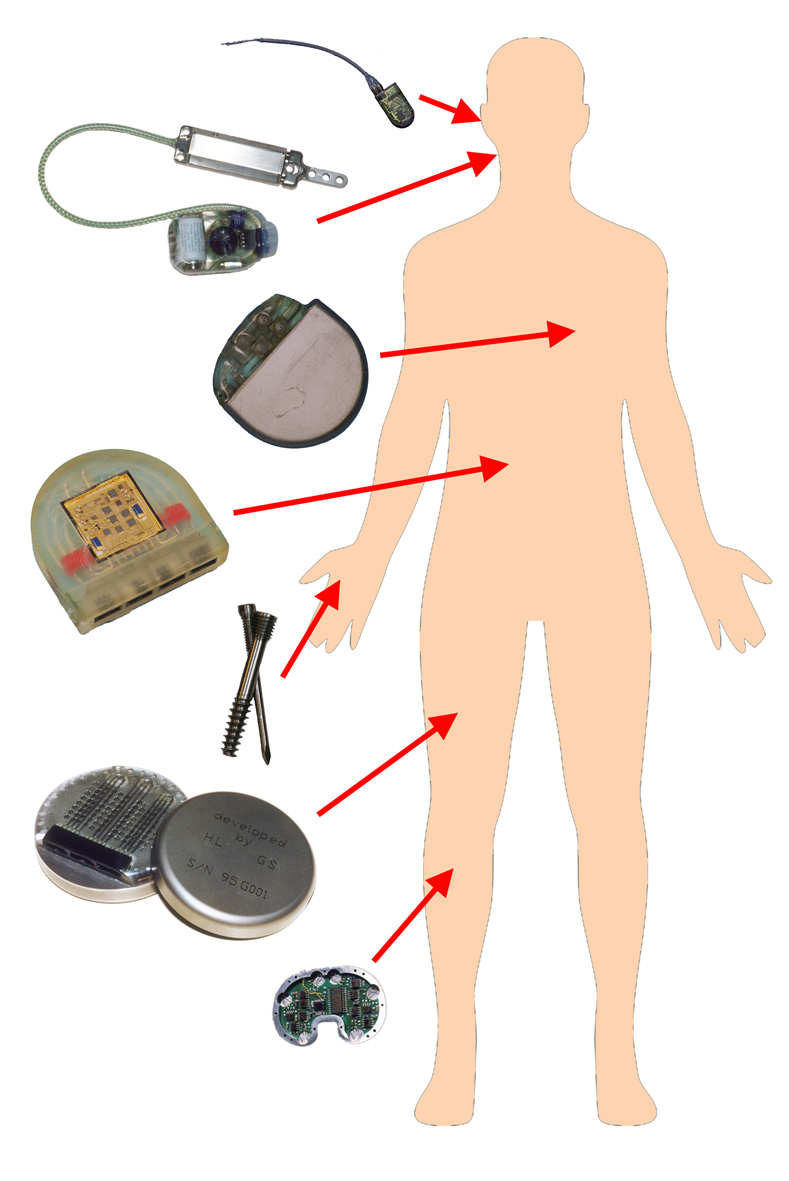
The development of Implants requires knowledge in the field of mechanics, electronics and software engineering, high-level production technology, material technology, and testing. All these domains have to be combined to build long term stable implants which can reside for month and years inside the body without the loss of functionality. Pushing a prototype towards a clinically relevant product requires excellent clinical and industrial partners, cooperating within preclinical and clinical studies in the frame of regulatory affairs.
Material technology and mechanics
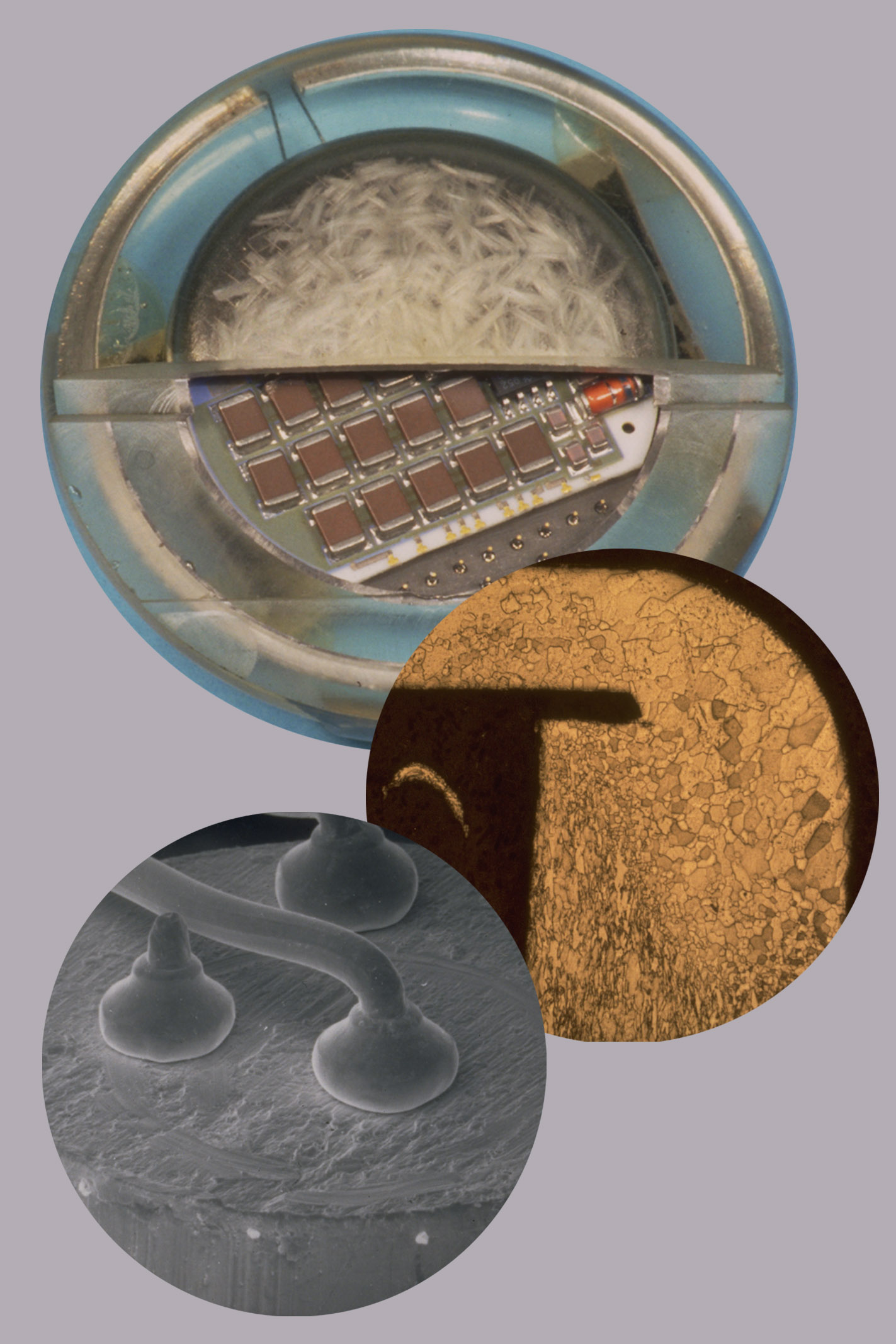
It all starts with the selection of the proper material. It must fulfill many requirements first and foremost biocompatibility and bioresistivity, followed by mechanical and temperature stability and the ability to survive the sterilization process. Classical manufacturing processes take advantage of CNC machines and molding technology. Additive manufacturing with the possibility to freely design implant geometry, implement intelligent surfaces, and adaptive materials open a new road towards precision and personalized medicine bringing diagnosis and treatment to a new level of highly individualized patient care. Moreover, multi-modal imaging (3D printed models) help to design implants in a way that they fit perfectly to the target locations inside the body.
Electronic and software design
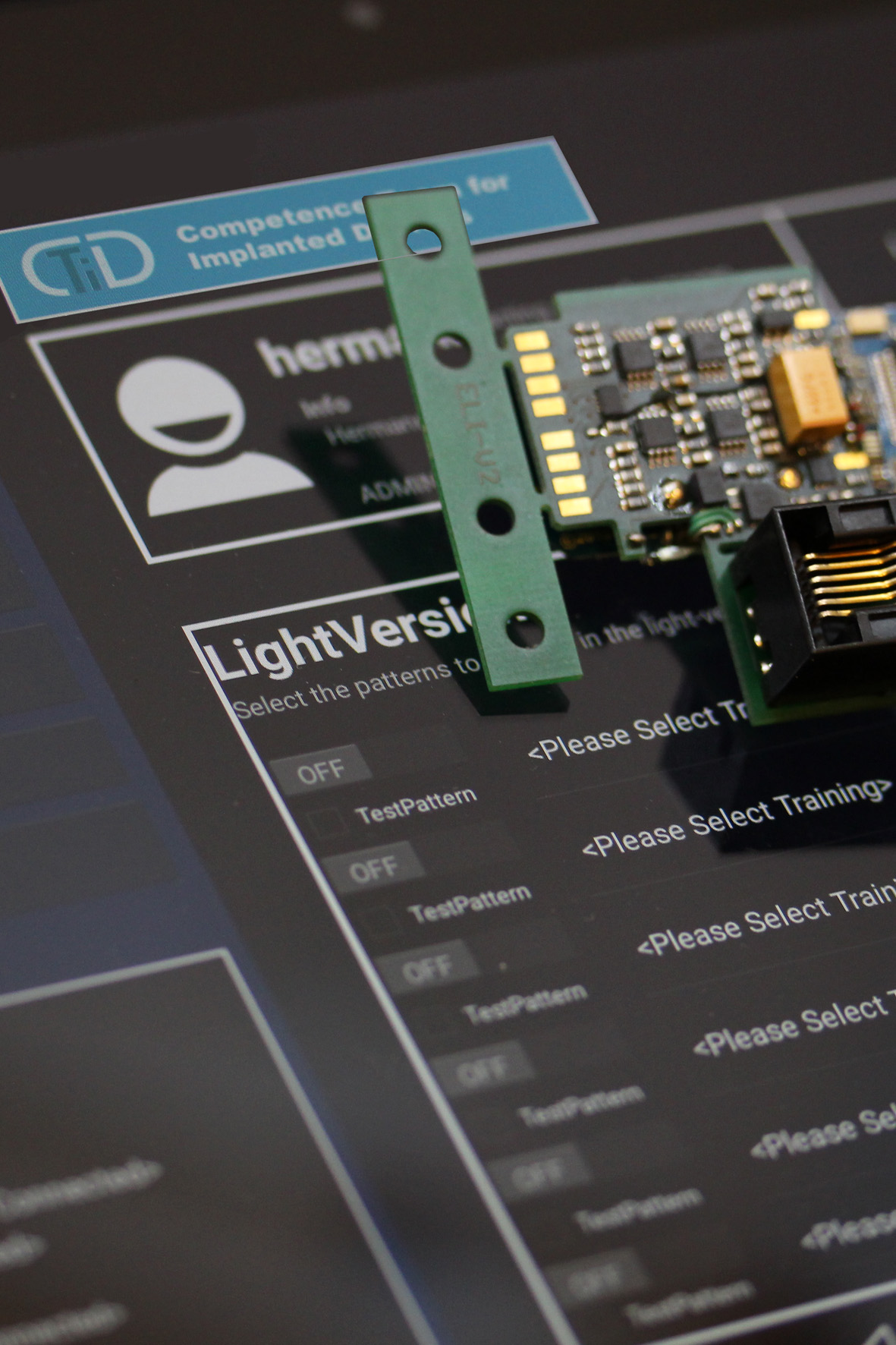
Optimized volume and low energy consumption, especially in battery-powered devices, are the most critical factors when designing electronics for implantable devices. State of the art technologies like SMD, chip on board, and ASIC are consequently used to reach these goals. Cleanroom technology is required when it comes to manufacturing devices that contact living tissue. Another important task is two way near field communication through the skin and underlying tissue. Controlling the device and reading out compliance data are essential measures to increase device safety and are the key to continuous improvements. Close cooperation between hard- and software engineers is the only way to implement all optimization strategies efficiently.